Continuous Shot Peening Method Pdf Wheelabrator Dt Continuous Rocker Barrel
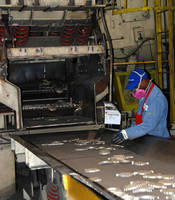
Burlington, ON - (January 27, 2009) - The Wheelabrator® Continuous Rocker Barrel machine is designed for high-performance in-line cleaning of castings and forged parts. To satisfy production requirements ranging from less than 5 tons/hr to over 25 tons/hr, a variety of machine sizes are available with blast capacities selected to match the specific cleaning requirements.
In December 2002, Neptune Technology Group Inc., the largest, leading supplier of brass water meters, installed a 3 wheel Wheelabrator Continuous Rocker Barrel at its Tallassee, Alabama facility. Prior to this machine installation, the brass water meters (which are foundry cast using the green sand cast process) were cleaned by one of two Tumblast® (28 cu.ft) systems supplied by Wheelabrator. Neptune also owns a Wheelabrator® Spinner Hanger which cleans large lost foam cast water meter housings. Even though Neptune's Rocker Barrel machine has 3 blast wheels, for normal production requirements, Neptune operates efficiently with only 2 blast wheels. From the control panel, the operator selects which blast wheels will be in service. Alternating the blast wheel selection lengthens the maintenance intervals between blade changes for all 3 wheels. This also extends the life of the barrel liners and curtain seals for reduced maintenance costs. Having an extra blast wheel ensures minimal downtime due to wheel related problems, which is a significant advantage on a continuous blast machine.
After in-line sand shakeout and cooling, the castings are delivered to the Rocker Barrel via an inclined belt and shaker load conveyor, providing process improvements to the overall automated operation. The drive that rocks the barrel is controlled from a touch screen on the operator panel. An adjustable range of rocking motion ensures different shaped castings can be tumbled satisfactorily. A separate mechanism sets the adjustable decline angle for controlling the flow of castings through the machine. The control system allows both manual and automatic selection of the work conveyor parameters to compensate for changes in part configurations and cleaning requirements. The combination of a variable decline angle and rocking angle for the work conveyor barrel provides a high degree of control for achieving effective blast coverage. Depending on daily production requirements, the rocker barrel satisfies Neptune's surface preparation requirements in 1 to 2 shifts.
In 2007, Neptune upgraded its Rocker Barrel system through an EMP upgrade by installing front support rolls with liners and 2 new rolls to the back-end of the machine. A barrel liner rebuild package was installed, allowing Neptune to replace individual liners for an overall savings of time and money.
"Neptune is very pleased with the Rocker Barrel and we are currently looking at a new EMP upgrade for further improvements", states Deric Murphy, Senior Manufacturing Engineer.
Equipped with Wheelabrator EZEFIT® blast wheels, the Continuous Rocker Barrel provides effective part cleaning with lower operating costs. Neptune's Rocker Barrel installation was an added process to streamline its overall automated operation and provide improved processes. Heavy-duty EZEFIT® wheels provide long-wear life and are designed for ease of maintenance. To help meet various surface finish requirements, interchangeable blade sets provide larger or smaller wheel diameters for a low cost way to adjust the abrasive velocity. An option for variable flow abrasive valves offers additional adjustment capability for fine tuning the cleaning operation and controlling operating costs.
Handling part conditions from foundries and forge plants, including sand, scale and other contaminants, the Continuous Rocker Barrel is built to withstand these challenges. An abrasive recycling system including lower shaker reclaim conveyor, bucket elevator, rotary screen, double lip air wash separator and storage hopper, recovers, cleans and stores the blast media. Magnetic separation is also available for foundry requirements. The work conveyor barrel is a self-draining, variable slope design with a heavy manganese frame and replaceable manganese liners. The Wheelabrator® Continuous Rocker Barrel is designed for use with long-lasting steel shot blast media.
Wheelabrator Group is a global provider of surface preparation and finishing solutions. Committed to offering the broadest array of technologies, products, services and technical know-how, Wheelabrator Group works closely with customers to deliver the best solutions for their specific requirements. The company's strategically located and electronically linked offices allow Wheelabrator Group to provide unrivalled customer service and support worldwide. For more information on Wheelabrator, visit the web site at www.wheelabratorgroup.com or e-mail info@wheelabratorgroup.com.
Wheelabrator products are protected by patents issued and pending in the United States and other countries.
FOR FURTHER INFORMATION:
Pamela Akin
Marketing Manager
Wheelabrator
800-544-4144, ext. 2295
Pam.Akin@wheelabratorgroup.com
MEDIA CONTACT:
Flammer Relations, Inc.
770-383-3360
Laura Everett:
Laura@flammerpr.com
More from Packaging Products & Equipment
Source: https://news.thomasnet.com/companystory/wheelabrator-rocker-barrel-machine-providing-high-performance-continuous-cleaning-823890
0 Response to "Continuous Shot Peening Method Pdf Wheelabrator Dt Continuous Rocker Barrel"
Post a Comment